Test equipment for the Wind Farm sector; improve efficiency, reduce cost & extend the life of your assets
Test equipment which is of particular value in wind farm applications including Anemometers / Rotor Bearings / Generators, Pitch Control / Gearboxes / Gearbox Cooling Systems , Pad-Mount Transformers MV Circuit Breakers, and Substations / Transmission.
Wind Farm Test Equipment
Wind Turbine Components - Anemometers / Rotor Bearings / Generators
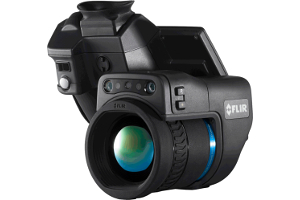 |
FLIR T1020 HD Thermal Camera - Wind Turbine Testing |
Maintenance teams utilise thermography to check electrical connections |
Features |
Anemometers: critical to understanding wind speed and direction, and by extension, optimising a wind turbine’s energy output (these can be mounted at various heights to collect accurate wind speed data, transmitting rotation data to a control centre that’s responsible for positioning the turbine into the wind for maximum efficiency).
|
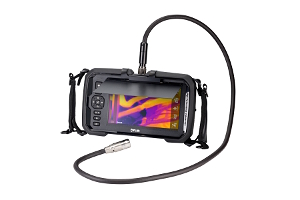 |
FLIR VS80-IR21 Videoscope Kit - Wind Turbine Testing |
See into the cramped bearing casings |
Features |
Rotor Bearings: Wind turbine components are susceptible to wear and can break down, especially the rotor bearings: a series of bearings within the rotor shaft that connect the wind turbine blades to the gearbox. Ensuring proper operation is critical to maintaining operational efficiency and asset health. An IR videoscope probe allows you to see signs of overheating. A vibration meter or remote vibration monitoring system could detect signs of mechanical failure via vibration analysis.
|
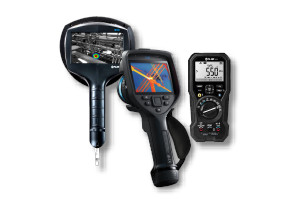 |
FLIR E96 Thermal Imager & IM75 Insulation/DMM - Verify the health of wind turbine mechanical and electrical components
|
FLIR Si124-PD Acoustic Imaging - Find problems before failure |
Features |
Wind Turbine’s Generator: takes output from the gearbox and produces electric power. These complex systems can include commutators, slip rings, coils, cooling systems, and more - all of which require regular inspection to ensure proper operation and asset health. Acoustic imager: inspects electrical systems to detect problems before breakdowns occur. Thermal cameras and digital multimeters: verify the health of mechanical and electrical components.
|
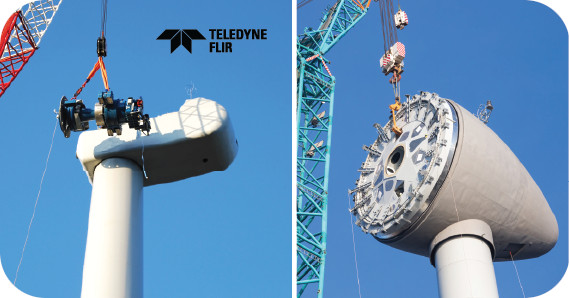
Wind Turbine Components - Pitch Control / Gearboxes / Gearbox Cooling Systems
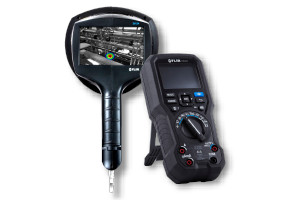 |
FLIR DM286 Industrial Multimeter - Check voltage levels and find electrical hot spots |
FLIR Si124-PD Acoustic Imaging - Find problems before failure |
Features |
Pitch control systems: control a blade’s angle, matching it to the direction of the wind in order to adjust speed of rotation, allowing optimal efficiency (this reduces mechanical load). The pitch control systems include VFDs ensuring a gradual start/stop preventing shock loads. The VFD, motors, and hydraulic components of this system should be checked frequently.
|
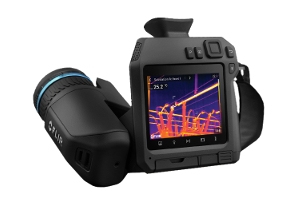 |
FLIR T800-Series & T1020 Thermal Camera |
Essential to check temp. / condition of gearbox bearings, gears and components |
Features |
Gearbox: connects the rotor shaft to the power generator and increases the rotations per minute (RPMs) to optimise power generation. The gearbox must function efficiently in demanding weather conditions and under loads, vibrations, and temperatures that continuously change. Temperature and condition of bearings, gears and components is essential to operational efficiency and asset health.
|
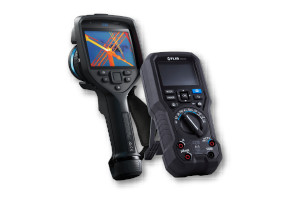 |
FLIR DM286 and E96 / E8-XT Thermal Imagers |
Regular inspections of wind turbines with thermal cameras and DMMs help avoid failure/downtime |
Features |
Gearbox cooling systems: maintain a consistent temperature within the nacelle to ensure the life expectancy of all the components. The process of energy conversion along with solar radiation can generate heat that could damage the components. Regular inspections with a thermal camera, as well as electrical inspections with a digital multimeter, can provide several months of warning time before failure, avoiding costly downtime.
|
Power Utility Maintenance - Pad-mount Transformers / MV Circuit Breakers
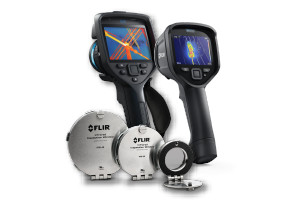 |
FLIR IR Windows and E96 / E8-XT Thermal Imagers |
Find hot spots that indicate overheating parts or signs of electrical resistance and mechanical wear so you can begin repairs immediately |
Features |
If a transformer overheats and fails, it can lead to expensive repairs and potential power outages. Regular monitoring using advanced diagnostic thermal imaging cameras can help you easily inspect and monitor the temperature distribution on the outside surface of each transformer to catch impending failures before they occur.
|
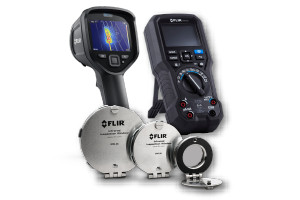 |
FLIR DM285 Industrial Multimeter, IR Windows & E8-XT Thermal Imager |
Frequent inspections: checking for loose or damaged connections |
Features |
Medium voltage (MV) circuit breakers connect the low voltage wind generated power through a step-up transformer to the bus of a high voltage/medium voltage substation and can be installed either above or below ground. While above-ground MV circuits are easier to access, they require frequent inspections with a thermal camera and test and measurement tools to ensure none of the connections are loose or damaged. Below-ground MV circuits are costlier to install but require less maintenance. Inspectors may need to check these breakers occasionally for splice failure or ground faults. The visual inspection of poles and mounting equipment is also need to ensure the collection system is in good working order.
|
Power Utility Maintenance - Substations / Transmission
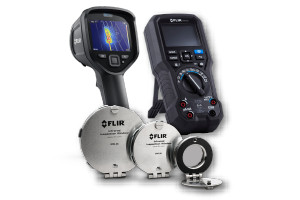 |
FLIR DM285 Industrial Multimeter, IR Windows & E96 Thermal Imager |
Frequent inspections: checking for loose or damaged connections |
Features |
Substations contain the most typical equipment found at a wind farm, including transformers, breakers, switches, and relays. If any of these systems fail, the entire transformer will shut down, costing millions in added overtime pay for workers and expenses to expedite repairs. Regularly scheduled electrical inspections with thermal imaging cameras along with surveys for SF6 insulation leaks with a gas detection camera will ensure equipment keeps working and wind farm operators meet safety regulations governing their equipment. Most wind farms perform these tasks during the low-wind season to reduce their loss of generation and revenue.
|
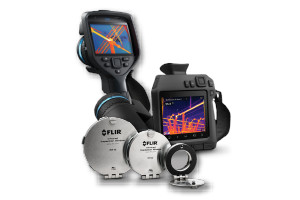 |
FLIR T1020 & T-Series (FlexView Dual FOV Lens) Thermal Imagers - Get the full picture of potential problems |
FLIR Si124-PD Acoustic Imaging - Find problems before failure |
Features |
Unplanned transmission line repairs can easily cost millions, so it’s important to regularly inspect every connection to ensure that they are in working order. Every system has a lot of small connections, often located high up out of reach. Connections get hot before they fail. Conducting regular surveys of substations and transmission lines using a thermal imaging camera can give you a full picture of potential problems. You can visualise partial discharge or measure the temperature of overheating connections and diagnose problems before outages occur - minimising the cost of repairs, maximising equipment life, and keeping the power on for customers.
|